May 23, 2023 • 4 min read
Decarbonizing chemicals: overcoming the challenges producers are facing
How can the chemicals industry reach net zero by 2050 while still delivering everything the modern world needs, and wants?
“Today’s chemicals industry is built on cheap and abundant fossil hydrocarbon feedstocks and energy,” says Chris Mole, Global Sector Lead for Chemicals and Fuels. “But the industry needs to play a role in addressing climate change, with new chemistry based solutions for a sustainable world. And to make this change, the industry needs world class engineering solutions.
“Having spent over 30 years working in the chemicals and fuels sector, for both licensors and project delivery companies, it’s evident that the pace of change in the chemicals industry is faster than ever before,” he says. “Producers are embracing the challenges of creating a net zero future.”
The role of alternative feedstocks
“In the first instance, we need to address those chemicals currently producing large carbon emissions during production. For example, traditional routes to hydrogen are starting to be managed with carbon capture – known as low carbon hydrogen – or by changing to renewable powered electrolysis, to produce renewable hydrogen,” says Mole.
“We’re also actively working with customers to convert to bio-based feedstocks where that makes sense.”
A traditional example of bio-based feedstocks is converting sugars to make alcohols or acids and then advancing them to polymers.
“Current thinking has the industry developing renewable naphtha from the same refinery processes that manufacture renewable diesel and sustainable aviation fuels or developing bio-oil from the pyrolysis of woody biomass,” continues Mole. “These newer options would enable existing crackers to produce bio-ethylene and bio-propylene.”
Decarbonizing old processes
Process changes are initially focusing on electrifying energy usage such as steam generation, and then supplying that electricity from sustainable sources.
“The first efforts in decarbonizing processes will be applied to existing manufacturing plants, to make the most of that existing capital investment. The solutions need to be tailored to each process and can include carbon capture, utilization and storage, energy efficiency, fuel switching, and circular resource recovery.
For greenfield processes, we have to consider that a new chemical plant being engineered now will still be operating in a net zero world in 2050. So, we need to design in the latest proven decarbonized technologies and the provisions to upgrade as emerging lower carbon technologies become available and economically viable.
The role of resource stewardship
The chemicals industry takes product stewardship and end of life considerations seriously. It also has a strong track record in areas like the disposal of dangerous chemicals.
However, the waste and litter associated with used plastics has now become a significant social license issue for our customers.
“Plastics are a great example where we’re working with customers to convert this previously considered waste into energy, or feedstock, or fuel. There are a variety of existing and new processes being proposed, and we’re involved in scaling up first of a kind (FOAK) technologies.”
First of a kind: from vision to market
“Scaling up FOAK solutions from a lab, pilot, or demonstration plant to industrial is complex,” says Mole. “We work alongside our customers at different project stages, from technology development right through to commercialization.”
Geert Reyniers, Senior Director for Process and Technology describes the unique considerations of these novel technologies.
“When we consider the variety of technologies being introduced to decarbonize products and processes, FOAK expertise is essential for navigating the energy transition successfully. Whether it be one of the circular processes in the diagram below, or another transformational process, the structured approach is the same.”
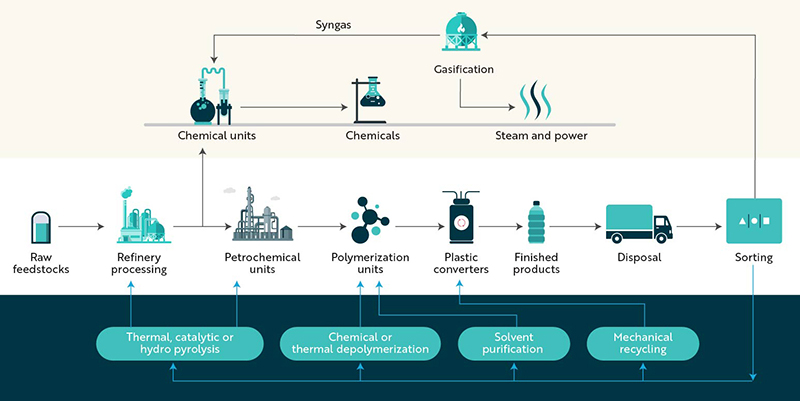
This requires a process for assessing the technology and then systematically moving it through development. This includes the design and engineering itself, factoring in sustainability, the utilities and logistics required, the fabrication and construction, all the way through to ongoing operations.
“A learning mindset is essential to bring the experience of the past, and includes insights and improvements at each assessment stage,” says Reyniers. “At the same time, risk management is always a focus, alongside innovation. Successfully implementing and commercializing these new technologies is the goal for our customers, for us, and for a net zero future.”
Sustainability is more than just an environmental viewpoint
The service we offer our customers in the chemical sector is more than just about the requirement to decarbonize.
“Our global community of consultants, scientists, engineers, and digital experts work with our customers to consider the sustainable management of water and land. And oversee the vital interactions with local communities, indigenous owners, and governments,” says Mole. “We believe that sustainability goes beyond simply an environmental viewpoint.”
Our people also apply the latest sustainability methodology to project management, supply chain, engineering, and construction.
“We support our customers to reduce the environmental footprint of their plants and future operations,” he says. “And the ultimate goal is helping them meet their net zero commitments.”
The path to net zero is clear
Mole believes that the global climate response demands vision, innovation, and collaboration. He thinks a lower carbon future for chemicals is possible. And that it can sustain the environment and our lifestyles, all while meeting social expectations.
“It’s about visualizing and working together along the supply chain to drive technological advancements at pace and scale, implementing strategies and policies and utilizing the resources we have in a responsible way.
“We know we’re on a journey with our customers,” says Mole. “And more than ever, we’re committed to helping them align their operations with a more sustainable future.”