December 06, 2021 • 4 min read
Providing EPC services for OMV's Pohokura Depletion project
How we supported the Pohokura gas field in New Zealand with more sustainable solutions
As the New Zealand energy sector focuses on transitioning to net-zero carbon emissions by 2050, natural gas has a key role to play in delivering a more sustainable future during this time.
The Pohokura gas plant is unique as it’s a remote operated facility comprising an offshore platform and onshore gas/condensate plant. It’s operated by OMV New Zealand, 20 km from the site in a central control room in New Plymouth.
Keeping gas production in New Zealand going
The Pohokura field is a depletion drive reservoir. Since the gas pressure falls with the extraction of the gas originally in place, the Pohokura field had recently reached the point where inlet compression was needed to continue production from the field.
This required the installation of a 10MW centrifugal compressor upstream of the existing Pohokura gas plant. Plus, the construction of a new power supply, two substations and integration into the existing gas plant while it remained operational.
However, integrating a new compressor with an existing plant created several challenges.
“The new compressor’s interaction with the existing plant needed to be tested fully before it was made operational. This was to make sure all safeguards were operating correctly, without causing costly downtime to the existing plant,” explains Mark Hatch, Project Manager. “Construction had to be carried out within the operating plant and in the area that the Ngāti Rāhiri Maori tribe are traditional guardians over. Both required additional levels of protection.”
Delivering sustainable solutions
We delivered the engineering, procurement and construction for the Pohokura Depletion Project – this included the largest variable speed drive electrically driven compressor operational in New Zealand.
“We're focused on making sustainable transformation a reality,” says Hatch. “That’s one of the reasons why we selected an electric compressor rather than a traditional gas turbine driven compressor. The electric compressor takes advantage of the 80 percent renewably sourced electricity in New Zealand and helps reduce CO2 emissions.”
Another important feature of the project was the installation of a new power supply. “Previously, power interruptions caused frequent production trips resulting in flaring, loss of product and wasted energy,” says Mark “The new power supply would increase resiliency and reduce the CO2 emissions associated with power interruptions.”
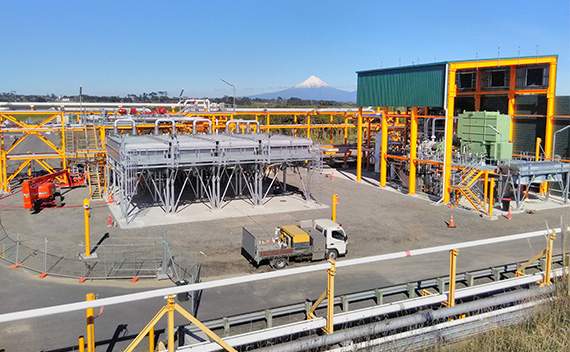
DC compressor, air coolers and pipe rack (view south)
COVID-19 response
Our team worked with OMV as a single integrated team. This meant that when COVID-19 hit and construction was halted during a country-wide lockdown, we were able to coordinate a fast response to keep the project on track.
Once construction work could start up again, strict control measures were put in place. This included a COVID-19 specific virtual induction, daily health screening, contract tracing, setting up trade work bubbles and additional facilities to allow social distancing, and enhanced site hygiene.
“We developed a COVID mobile app for the daily health screening,” says Hatch. “This streamlined the process and made sure that it didn’t delay the sign-in process of the construction crew each day, while protecting the health of our people.”
Finding digital solutions
The app was not only digital solution the the team used to keep the project moving forward. With overseas travel restricted, the team needed a way to replace in-person visits to the site.
“The pre-commissioning of the compressor anti-surge control system was carried out remotely, through collaboration between us, OMV and ControlCare,” explains Hatch. “We had to overcome many risks to achieve this. For example, the cybersecurity hazard because of the remote connection into the plant’s safety instrumented system and distributed control system.
“However, our use of digital and collaboration saved multiple overseas trips and quarantine periods and significantly reduced the pre-commissioning duration. It also prevented unwanted and costly schedule delays for the customer.”
Our digital expertise also allowed us to mitigate the risk of the compressor causing interruptions to gas production, plant downtime or revenue losses when it was started. “We developed a digital twin to model the operation of the existing plant with and without the new compressor,” says Hatch. “This included the transition of the new compressor into service during commissioning. The digital twin allowed us to test the compressor without impacting on plant production. It also meant we could train operators on the system ahead of commissioning.”
Respecting local communities
The project was delivered primarily using Taranaki-based expertise and labor, strengthening our relationships and knowledge in the areas. And while our focus was on making sure the project was a success, we also formed a strong relationship with the Ngāti Rāhiri Maori tribe.
“We had consultations and regular communication with Ngāti Rāhiri throughout the whole process. And when any excavation happened, Ngāti Rāhiri observers were brought in to look for buried artifacts,” says Hatch. “On completion of the project, Ngāti Rāhiri presented the site with stone carvings for the entrance, which represent two Ngāti Rāhiri kaitiaki (guardians) – Rāhiri Ki Uta (Rāhiri Inland) and Rāhiri Ki Tai (Rāhiri Oceanward).”
Worley New Zealand project success
We completed the Pohokura Depletion Compression project NZD 2.8 million under budget and six weeks early, despite a seven-week COVID-19 lockdown. It required 130,000 workhours of site construction and was delivered with 445 days with zero harm.
“The compressor start-up was flawless. There were no compressor trips or interruptions to the production station,” says Hatch “Looking back, it’s a credit to the strength of the team that we achieved what we did in such exceptional circumstances. We’ve not only extended the life of the Pohokura gas field, we’ve helped the plant reduce its emissions and increase reliability at the same time.”
The Pohokura Depletion Compression project was a finalist for the 2021 Worley Pinnacle Awards.
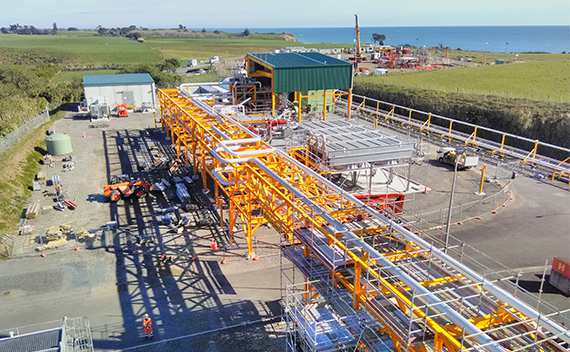
DC process pipe rack and equipment (view west)