November 04, 2020 • 3 min read
Engineering and building MEGlobal’s ethylene glycol facility
How we helped deliver the first commercial-scale ethylene glycol facility in the US
Clothing. Water bottles. Construction materials. Antifreeze. These are just some of products we rely on daily that ethylene glycol (EG) is an essential ingredient in.
Recently, the US Gulf Coast has become an attractive place to produce EG. This is due to the emergence of shale gas plus predictions that lower priced natural gas will continue. MEGlobal – a wholly-owned subsidiary of EQUATE Petrochemical Company – picked Oyster Creek in Freeport, Texas as the location for its first commercial-scale EG facility, manufacturing monoethylene glycol and diethylene glycol.
The facility has a nameplate production rate of 750,000 metric tons of EG per annum. Like any success story, the facility is a true team effort. The new plant is located close to an ethylene cracker complex, which supplies the facility with ethylene. A commercial gas supplier provides the oxygen and nitrogen to MEGlobal’s plant and recaptures CO2 from the facility. Waste CO2 is then recycled in other commercial uses and reduces the plant’s carbon footprint.
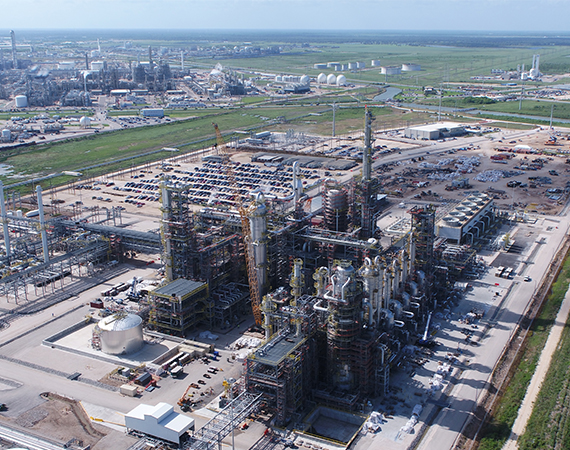
For its first manufacturing unit in the US, MEGlobal selected METEOR™ catalyst from The Dow Chemical Company as well as Dow’s leading process technology for world-scale ethylene oxide (EO) and EG facilities. As part of the licensor team, we worked closely with the technology licensor as it developed the licensor package for its EG technology. Our Reading office in the UK provided engineering and design services for the technology licensor.
Our relationship extended from project planning into the front-end engineering design (FEED) phase of the project, which further developed the licensor package data and added in the offsites and utilities facilities. It then progressed into engineering, procurement and construction management (EPCM). We also supported MEGlobal with the commissioning and start-up phases through to initial production.
Our Reading, Mumbai, and Houston offices shared the work for this project. The overall engineering and design effort was supported by multi-office project execution, with our Global Integrated Delivery (GID) team in Mumbai completing 72 percent of the engineering and procurement hours and over 95 percent of all project deliverables.
A project that has not been seen in the last two to three decades on the US Gulf Coast for excellence in project execution.
Working as one team
With high numbers of staff working on the project’s engineering at any one time, integration between the global offices was vital. The Mumbai and Houston offices adapted their hours to allow a handover period each day, so that engineering could continue 24 hours a day. All offices used document control and 3D modeling tools to support this.
Several experts from MEGlobal, including engineering and manufacturing personnel, rotated into our Mumbai office to lend insight to the project. This customer commitment reduced the time it took to troubleshoot issues and agree to a way forward.
Over 200 worldwide vendors supplied goods to the project, and we implemented an extensive vendor management program to make sure that all equipment and materials we used met project requirements. And with over 50 site contractors, we applied advanced work packaging to make sure all the equipment and material were installed in an orderly and efficient way.
The project achieved 3.7 million hours of continuous safe work, while maintaining an aggressive schedule. That schedule meant that the construction was completed in under two years when projects of this scale often take over two and a half years. The project achieved mechanical completion and produced on-spec EG ahead of schedule.
The one team approach to the project, along with the use of digital construction technologies, meant that Worley delivered a best-in-class project for MEGlobal. It also earned an award of merit at ENR’s Global Best Projects awards, and ENR’s Regional Best Project in Texas and Louisiana for the Power/Industrial category.